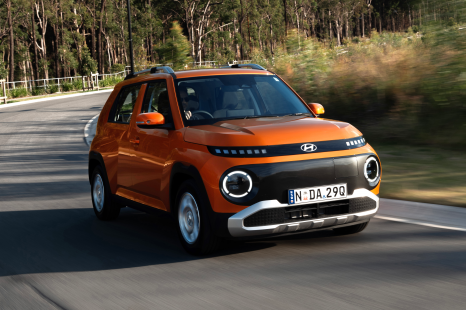
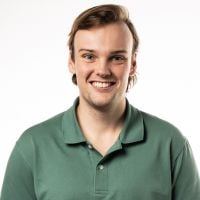
Josh Nevett
5 Days Ago
Founder
Almost every week we publish spy photos of upcoming models, with manufacturers going to huge lengths to conceal the appearance of their new-generation products both inside and out.
We had the chance to join Ford on a development drive for the 2023 Ford Ranger and Ford Everest last year in the Victorian high country, and wanted to get a better idea of why prototype vehicles look the way they do.
Firstly, the vehicle development process often begins years before a vehicle is ever built.
These days that period extends even further thanks to advancements in computer design and simulation, meaning a physical vehicle doesn’t need to be produced until much later in the piece to test out design theories.
We exclusively revealed back in May 2020 that Ford would be going all out with engines and interior technology, but it wasn’t until we (also) exclusively revealed spy images in July 2021 that we confirmed everything would actually be happening.
While none of this is unique to Ford, we wanted to explore some of the things manufacturers do behind the scenes to develop a new vehicle.
A common theme amongst prototypes is the use of camouflage paint, stripes and wraps to prevent body contours from being seen. This type of pattern also makes it hard for photographers to lock focus on a vehicle as the camera hunts for a contrast difference to latch on to.
The wrap is often also joined by padding or artificial panels that exaggerate body parts and surfaces. In Ford’s case with the Ranger and Everest, wheel arch padding was used to make wheel arches look bigger to throw people off the scent.
Depending on how far down the line a prototype is, it sometimes uses the body of the outgoing model or in some cases it uses aftermarket LED lights while the proper headlight or tail light design is being finalised.
In our video above we reveal the velcro headlight covers that help prevent the headlight design from being revealed. The caveat to this setup is that the lights all still need to be functional for the vehicle to be used on the road.
Ford revealed that there were also times when the headlight covers needed to be removed to test the matrix LED features on the car. This was done at night time at Ford’s proving ground in Victoria where the vehicle could be driven sans headlight concealers to make sure everything was working correctly.
Test cars are often riddled with colour coded stickers and codes. To the naked eye this often doesn’t mean much, but these are used to identify internally within Ford what function that prototype serves.
Some prototypes exist solely for the purpose of testing headlights, or suspension, or aftermarket accessories, and they can easily be identified using their stickers.
Pop the bonnet on a prototype and you’ll often find an assortment of cables and other random accessories fitted for the purpose of testing.
The prototype we checked out had a number of thermocouples running to various engine parts and accessories. These all feed back to a data logger that keeps tabs on what’s going on around the car. In the event of a failure or problem, they keep track of exactly what went wrong so engineers can sort problems out.
During our durability drive, one of the Raptors broke a fan belt while accelerating up a hill. This particular car was used for durability testing and had racked up some 150,000km within a six month period.
This issue was captured by the data logger and the team was able to investigate further to figure out what caused the issue so that it doesn’t happen again.
An item that Ford championed as part of Raptor and Bronco development was creating a camouflage for the rear suspension. It was designed to hide what was going on beneath the rear and it was a clever engineer within Ford that came up with the idea of using brush heads wrapped around the diff to conceal what was going on.
This is where things get more interesting.
The whole point of preventing prying eyes – especially early in the development process – comes down to stopping competitors from seeing what a brand is doing. If you look at Everest and Ranger for example, the technology within the cabin immediately propels these vehicles to class-leading status.
If the likes of Toyota or Isuzu for example saw this information early enough, it would give them time to pivot from what they had planned to do and perhaps throw more effort at it.
So it goes without saying that Ford has developed a system that allows the interior to remain covered when not in use. Protocol dictates that whenever the vehicle is being driven in public or within earshot of passers by, the interior must remain fully covered.
And to further conceal the fact Ford was using a large vertical screen within the Ranger and Everest, each test vehicle had a smaller opening at the top that made it look like the screen was a more traditionally sized unit.
It wasn’t until we captured footage of the screen being fully uncovered that it confirmed our earlier thought that it was a vertical screen.
Further to this, prototypes often have unfinished panels that feature smooth textureless plastics that are placeholders until an interior is complete for further builds. One example of this was an Everest on the development drive that didn’t feature the wood finish found in the final production vehicle.
Next to the driver is an ejector seat style button that is used to inform the data logger that an issue has been detected and that it should record the previous 30 seconds of data. This captured data is then transferred via the cloud back to base so it can be analysed by engineers.
It’s further backed up by a feature on Sync 4 that allows engineers to record voice memos about certain functionality issues that are also captured and sent back to base via the cloud.
A final item inside the cabin we found curious was a giant emergency stop button on the dashboard. Hitting this kills all of the vehicle’s electronics and allows the car to be immobilised – in addition to triggering a data recording event.
It’s used in scenarios where there is a major or catastrophic failure that prevents the vehicle from operating.
It was great to get a brief behind the scenes look at how and why prototypes look the way they do.
There’s no denying that timelines and budgets are getting shorter and thinner, which is partly why so much effort is put into the predevelopment work before a car is even built.
And it’s always great to see a big investment in Australian design and engineering, especially for products like the Ranger and Everest, which will be sold in close to 200 global markets.
Take advantage of Australia's BIGGEST new car website to find a great deal on a Ford.
Paul Maric is an Australian car expert based in Melbourne, Australia. Paul is a founder of CarExpert.com.au & formerly part of the CarAdvice founding team.
Josh Nevett
5 Days Ago
Matt Campbell
4 Days Ago
Angus MacKenzie
3 Days Ago
Matt Campbell
2 Days Ago
James Wong
18 Hours Ago
Marton Pettendy
18 Hours Ago