
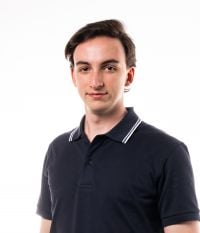
Max Davies
5 Days Ago
The Toyota New Global Architecture (TNGA) is the Japanese giant's take on modular platform sharing to rival the likes of Volkswagen’s MQB.
Contributor
Contributor
Toyota strongly espouses the notion of ‘kaizen’ or continuous improvement, and this corporate philosophy has enabled it to implement its vision of ‘making ever better cars.’
One of the more recent ways in which Toyota is undertaking kaizen is through the development of what it calls TNGA, an initialism for Toyota New Global Architecture. Ostensibly, this is a modular platform-building concept to create economies of scale, similar to the MQB, MLB and MEB platform toolkits that the Volkswagen Group currently uses.
However, Toyota claims that TNGA goes far beyond the engineering and design of the vehicle itself. Instead, it is a fundamental program of structural innovation that improves and modernises the Toyota Production System (the process by which Toyota builds cars) and enables the harmonisation of production planning and vehicle design.
As discussed in further detail below, TNGA-based vehicles currently on sale, or soon to be available, spread across the entire Toyota and Lexus line-ups and include everything from the Toyota Yaris to the LandCruiser 300 Series and Lexus LC. The first TNGA car to be introduced was the latest, fourth-generation Toyota Prius.
Designers and engineers of TNGA vehicles are able to choose between five different seat heights, a range of shared systems including powertrains and drivetrains, and associated mechanical components to design everything from hot hatches to large SUVs.
One of the primary benefits of TNGA from a production standpoint is far greater cost efficiencies and economies of scale brought about through the sharing of parts across vehicles.
Toyota claims the introduction of TNGA enables it to replace over 100 different platform variations used across its model lineup with just five, and over 800 distinct engine variants to be consolidated into just 17 different versions of nine engine families. These efficiencies are compounded by the firm’s claims that each TNGA part is up to 20 percent cheaper to produce than a comparable part from an older platform.
These advantages also yield further benefits during the production process. With greater parts sharing, multiple different models can be built on a single production line, with the distribution of these being flexible, and able to be altered quickly, based on customer demand. Not having separate production lines for each model of vehicle, in turn, also leads to smaller, more efficient single-storey factories for plants producing TNGA-only vehicles.
The development of TNGA has also allowed the firm to redesign some of the specific production equipment used to build these cars, with the company claiming to have built more compact and environmentally friendly paint booths, as well as a smaller and more efficient machine to produce soft-touch slush-moulded dashboards.
Perhaps more importantly, the set of advanced chassis technologies that TNGA brings to the table has also enabled Toyota to significantly improve the safety of its cars. TNGA vehicles are able to be fitted with the latest Toyota Safety Sense active safety and driver assist features, and also offer greater structural and torsional rigidity for improved physical crash performance.
Toyota CEO Akio Toyoda likes to brand himself as ‘Morizo’, and the firm’s ultimate master test driver, and it is with this level of focus and intent that Toyota has recently made substantial attempts to shake off its boring, ‘whitegoods on wheels’ image. TNGA is a crucial step on this pathway, with the brand claiming that having a low centre of gravity was an important cornerstone of TNGA development, alongside the strategic use of high-strength materials to improve rigidity without compromising vehicle weight.
By affecting the use of underlying mechanical parts only, Toyota claims that with TNGA it aims to preserve the same creative freedom and design flexibility that vehicle stylists might have if they were creating a car on a bespoke platform.
Much like how Volkswagen has the MQB architecture for transverse-engined vehicles and the MLB for longitudinally-engined cars, TNGA accommodates front-, rear- and all-wheel drive drivetrains and both transverse and longitudinal engine orientations across multiple vehicle classes.
The TNGA platform is therefore available in six different iterations, each classified by vehicle size. From smallest to largest (based on vehicle length), these are TNGA-B for light cars like the Yaris and Yaris Cross, following through to TNGA-C, TNGA-K, TNGA-F (body on frame variant for models such as the new LandCruiser 300 Series), TNGA-N and finally TNGA-L for full-size luxury vehicles such as the Lexus LS.
Of course, Lexus prefers to distance itself from parent Toyota’s branding, so will generally use the shortened form (e.g. TNGA-C is shortened to ‘GA-C’) of the platform name in its marketing materials.
Interestingly, whilst the GR Yaris is styled to resemble a simple 3-door variant of the otherwise humble Yaris, it actually sits on a Frankenstein hybrid platform that utilises TNGA-B for its front-end, together with the one segment larger TNGA-C for the rear of the car. Doing this helped Toyota engineers incorporate a more advanced independent rear suspension design for the GR Yaris, compared to the simple torsion beam used in standard versions of the car.
Two recently unveiled models that do not make use of TNGA are the ‘reimagined’ Lexus IS and the newly revealed GR 86. The new ‘reimagined’ IS is a heavy facelift, rather than an all-new car, and so continues to sit on the older ‘N’ platform (now replaced by TNGA-N in vehicles such as the JDM market Toyota Crown).
Meanwhile, the GR 86 is a joint development with Subaru, and whilst being a very substantial upgrade, retains the fundamental chassis design and mechanicals from the bespoke platform of the original 86/BRZ, whilst borrowing elements from Subaru’s own modular platform philosophy, the SGP (Subaru Global Platform).
In a similar fashion, the new Supra was a joint development with BMW and shares mechanicals, underpinnings and other technologies with the BMW Z4, and is therefore unrelated to TNGA models developed solely by Toyota.
Toyota is a proponent of both hydrogen and battery-electric vehicles, and on the BEV side, has already announced the next iteration of TNGA, namely e-TNGA. This is a bespoke EV platform that enables the brand to draw on the learnings from earlier TNGA developments, whilst taking full advantage of the space and packaging benefits available with battery electric vehicles.
Jointly developed with Subaru, the first pair of vehicles to use e-TNGA have already been announced, in the form of the Toyota bZ4X and Subaru Solterra.
These vehicles are highly likely to feature lithium-ion batteries, with Toyota eventually intended to switch to using solid-state batteries once R&D is complete towards the later part of this decade.
Take advantage of Australia's BIGGEST new car website to find a great deal on a Toyota.
Max Davies
5 Days Ago
James Wong
4 Days Ago
James Fossdyke
3 Days Ago
Gautam Sharma
2 Days Ago
Josh Nevett
22 Hours Ago
William Stopford
10 Hours Ago